The Roadblocks to Steel Decarbonization
The steel industry provides an interesting case study of the ability of different technologies to work together to decarbonize energy-intensive sectors. As a generator of 7% of global industrial emissions, the decarbonization of steel is critical for achieving desired carbon reduction targets. A report from Deloitte on the pathways to the decarbonization of steel found that emissions in steel production will need to fall by 90% to meet targets set by the Paris Agreement. With the majority of green steel being produced using blast furnaces, carbon capture and hydrogen use will likely prove to be critical for reducing emissions in traditional steel production methods. At the same time, it is unfeasible to think that all steel plants can suddenly switch to green hydrogen, so reducing current energy losses and inefficiencies will be a necessary step to be taken immediately.
By providing the energy required for the production process, steel manufacturers can significantly reduce carbon usage. Whether the production is done through coke production, blast furnaces, or iron-to-raw steel, carbon emissions are dominated by the ironmaking and steelmaking process as well as finishing and distribution. Steel manufacturers have made positive moves to limit carbon emissions, including widespread reductions by 2030 and commitments to net zero by 2050. There are technologies that can be used to reduce coal usage without forcing the adoption of expensive green hydrogen technologies or carbon capture efforts. One of the promising technologies is gas-based, which may be adopted by certain European steelmakers for the next decade until the believe that green hydrogen can compete on the international market.
The fear of green steel's inability to compete effectively in the international market was mentioned in a conversation with Kelvin Fu, the Chief Transformation Officer at Gunung Steel in Indonesia. As a possible solution, he mentioned the use of carbon credits to offset the cost of clean steel. There are important ways that Gunung Steel has set a standard for reducing carbon emissions in steelmaking. These include the use of an electric furnace, which produces a third of the footprint of a blast furnace. Using by-products of steelmaking to produce slag cement can contribute to circularity in the industry. Unfortunately, as Fu pointed out, the lower cost of blast furnaces and the ability to source iron ore and coke make traditional steel making significantly cheaper.
A large share of the responsibility to decarbonize steel production will fall to India and China, which use coal to power black furnace ironmaking. Policies have been implemented in China to ensure that iron and steel sector emissions should be reduced by 30% by 2030. India has also achieved reductions in emissions per ton through its energy efficiency certificates. For possible solutions, these countries could look at the work being done in Britain as they aim to replace the coal-based blast furnaces at Scunthorpe and Port Talbot with electric arc furnaces aimed at melting scrap steel into new steel.
Having heard the term "intermittent fuel" to refer to natural gas reasonably often, it is natural to feel a sense of doubt. However, certain steel plants are effectively preparing for the end goal of green hydrogen use by designing their gas facilities to be dual-fuel, meaning they can handle green hydrogen when it becomes an economically viable alternative. In the meantime, however, using gas over coal could still reduce roughly 75% of carbon emissions. It is worth noting the possible dangers of the switch to gas. As Europe continues to lead the way in green steel and make further switches to gas, they will continue to rely on a tenuous gas supply chain and possible geopolitical concerns.
In the United States, finding ways to decarbonize the steel sector and the lessons that this could play in other industrialization is more important now than ever. The US industrial sector's energy demand is anticipated to increase by 30% by 2050, growing emissions by 15%.
However, a conversation with Yong Kwon, Senior Policy Advisor for the Sierra Club's Industrial Transformation Campaign, offered the beginnings of a roadmap for decarbonizing steel in the United States: the work done in Sweden. Kwon explained that the work being done by Swedish companies such as Stegra and SSAB is demonstrating proof that steel decarbonization can work at scale. When asked what factors had led to Sweden being such an innovator in green steel, he offered several significant factors. These included state funding and vertical integration, which guaranteed available capital and downstream purchasers. Downstream partnerships with car manufacturers Volvo and Scania also provide consistent purchasing of clean steel for automobile manufacturing.

I then spoke to Michael Williams, a Senior Fellow for Energy & Environment at the Center for American Progress, who proposed a "Buy Clean" policy for developing infrastructure in America while promoting the burgeoning green steel industry. This would allow public financing to demonstrate proof of concept and provide capital for companies experiencing capital-intensive shifts to decarbonization. Providing subsidies to automakers using green steel could have the same effect, especially as electric vehicles continue to enter the market. The benefits of clean steel need not be relegated to the economic sphere. Reduced pollution from improved steelmaking policies can have health benefits in local communities and cause environmental remediation.
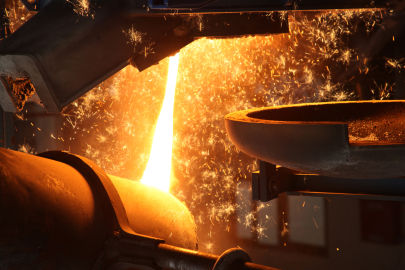
However, for these programs to work and for the government and private industry to work together, a certain level of transparency will be required. This was emphasized by Elizabeth Boatman, who spoke at length on the need for transparency between the different parties involved in the industry. As she explained, we cannot expect policies for downstream off-takers or regulators to plan for cost changes and adoption of technologies such as green hydrogen without steel manufacturers outlining their current costs and production targets. Likewise, it is unfair to expect steel manufacturers to risk costly adoption of green hydrogen or carbon capture without the confidence that users will purchase green steel.
As Sweden has offered a roadmap for US green steel development, a comprehensive approach to steel decarbonization and green hydrogen growth could assist global steel producers in Latin America and Southeast Asia. Exporting technology and knowledge to countries still developing their steel industry will create exponential reductions in steel emissions and set the standard for all industries to decarbonize.
Comentarios